Boat:
Rhumb Do
Date: October 2016
PROBLEM: Fridge partially defrosting, leaving
pool of water in bottom.
My small top
loading fridge is situated under one of the saloon seats, with the
Danfoss BD35F compressor, 101NO210 electronic control box and condenser
in an adjacent under seat locker, along with a Waeco Mobitronic EPS 100B
rectifier.
The compressor is
dual voltage, taking as it's supply, either 12 or 24 volts DC.
At sea, the
fridge uses the 12 volt supply direct from the house bank batteries via
a switch and fuse. When on 240 volt AC shore supply, the rectifier
supplies 24 volts DC to the electronic control box, which switches off the
12 volt supply and runs on the now 24 volts. It does this
automatically with no manual intervention.
It's a long drawn
out story which I have sort of described in the log
this month, but what I now know is the Danfoss compressor is fitted
with a little known, and very useful self diagnostics chip, the description of which I
will paste below.
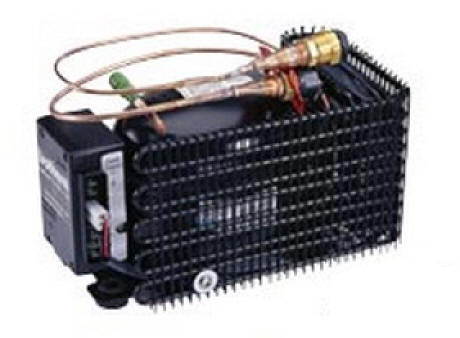
Danfoss BD35F Compressor.
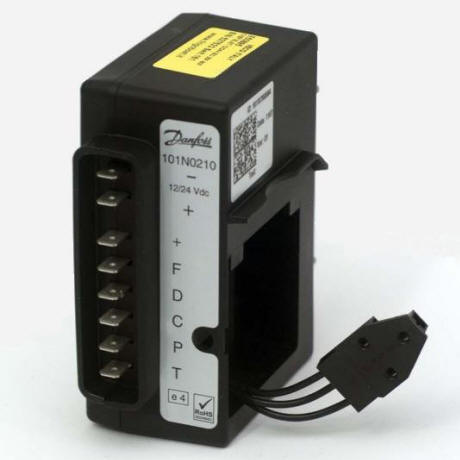
The Danfoss BD35 and BD50 compressors have their own
fault diagnostic allowing easy fault finding. The fault code will only
be shown when the compressor fails to start or stops.
Find the electronic control box pictured on the left
- it will be fitted to the side of the compressor
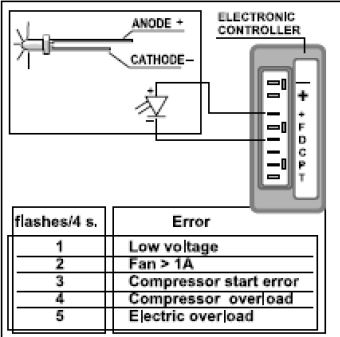
Start by Linking out the
Thermostat
To ensure the thermostat is not causing problems put
a link out between C and T terminals this will force the compressor to
run continually during testing.
Connect the LED fault diagnosis
circuit
If an LED light is connected between the small
positive (+) and D terminal on the control box, as shown in the diagram
, it will flash an error code if the compressor refuses to start.
Interpreting the results
1 Flash = Low Voltage
Indicates low voltage. Voltage at the incoming power
terminals on the Danfoss controller has dropped to less than 10.4v
(22.8v). Voltage must rise above the cut‐in voltage of 11.7v (24.2v)
before the compressor will attempt a re‐start. NOTE: If the initial
power applied at start‐up is less than 11.8v (24.3v), there will be no
fault code flashing on the diagnostic LED, but the compressor will not
attempt to start until the voltage has risen above 11.7v (24.3v).
a) Confirm the wire dimension is correct
If this is a new installation check the wire sizing:
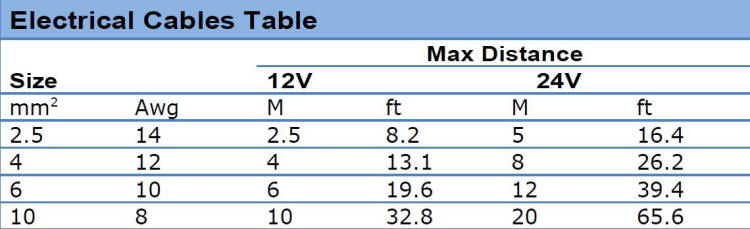
b) Test the Power supply
To properly test the power supply to a Danfoss
powered 12v or 24v system, the following testing procedure must be
carried out. This will establish whether the power supply feeding the
system is free of bad, loose and/or high-resistance connections.
Reading the voltage on the panel or at the batteries
is meaningless, as is the fact of a new installation or new batteries.
Size and the capacity of the battery bank is
irrelevant.
1. Turn off the breaker (or remove the fuse)
supplying DC power to the system.
2. Unplug one of the thermostat leads at the
controller.
3. Using a multi-meter, read the DC voltage at the
battery terminal(s).
4. Connect the multi-meter reading DC voltage to the
power terminals (+ and -) on the controller so that it can be left
connected and monitored.
5. Turn on the breaker (or install the fuse) to the
system.
6. Check that the voltage is the same as the voltage
seen at the battery terminals.
7. Whilst watching the multi-meter, reconnect the
thermostat lead and monitor the voltage continuously before, during, and
after the compressor starts or attempts to start.
Interpreting power supply results
If the power supply is free of loose, bad, and/or
high resistance connections, the voltage reading at 5 above will stay
very stable and only drop slightly when the compressor starts. As a
general rule, on a 12v system the reading should not drop below 12v.
If, when the compressor attempts to start, the
voltage reading drops significantly, a bad electrical connection should
be suspected. If the voltage drop is sufficient to fall below the 10.5v
(23v) cut-off built in to the controller, the compressor will stop. (At
this point the voltage may return to it s original reading.) The fan or
pump will continue to run for approx. 45 seconds and then the compressor
will attempt a re-start. If the voltage is then above 11.5v (23.5v) the
compressor will start or attempt to re-start again.
NOTE:
If the
multi-meter being used is a digital model that is slow to react, the
voltage may drop below 10.5v (23v) and then recover too quickly to
register on the meter. This can lead to the situation where the
compressor starts then stops from low voltage, the voltage returns to
its original value, and there being no significant drop on the meter.
If the compressor starts and runs OK but stops after
a short while, the voltage may be gradually dropping towards and below
the 10.5v (23v) cut-off point.
This should be easily identified on the meter.
If the nature of the fault is such that the voltage
reading at 5 above drops below 10.5v (23v) even before the compressor
attempts to start, a very bad electrical connection must be suspected.
This is because even the small load of the fan or pump relay, both less
than 0.5 amp (0.25 amp), is seemingly sufficient to reduce the voltage
considerably.
What to look for
A loose and/or high-resistance connection can be
anywhere in the supply between the batteries and the controller. i.e. a
bad breaker or fuse, a loose or corroded screw connection, a poorly made
or corroded crimp connection, a damaged section of wire, etc. A good
place to look first is the negative (ground) connection, especially on a
European-built boat. These tend to be multiple, common connections that
are added to over time.
2 Flashes = Fan draws more than 1 amp
a. Air cooled systems
The fan is faulty and drawing more than 1 amp.
Unplug the fan or water pump and restart the compressor.
You will need to replace the fan.
b. Water cooled systems
Unplug the water pump and restart the compressor to
confirm the compressor will now run.
If the system now runs it means the pump is drawing
more than 1 Amp. The system should be set up with the pump connected via
a relay or pump interface to prevent this happening.
If it is not, add a relay to the system.
If there is a relay/pump interface already fitted it
may have developed a fault and should be replaced.
3 Flashes = Compressor Start Error
This could still be a voltage error, due to a power
surge or similar, or (more usually) a faulty compressor controller.
First turn off the power to the unit for 1 minute to let
the system reset. Turn the power back on and see if the fridge runs.
If the system still fails to start, replace electronic
controller or send it to a reputable dealer for testing.
4 Flashes = Compressor Overload
Indicates that the compressor cannot reach minimum
speed of 1,850 RPM.
System has a blockage, possibly moisture that has entered the
refrigeration system or the compressor has seized (unlikely).
Send the controller to a reputable dealer for testing.
5 Flashes = Electric Overload
Indicates that the electronics heat sink has exceeded
212 deg F (100 deg C). This can be due to an overcharge of refrigerant,
water in the system, or excessive ambient temperatures combined with a
compressor operating under extreme load. A re‐start will be attempted
when heat sink has cooled to 170 deg F (80 deg C).
A guru of small BD compressors says:
Troubleshooting one of these units is simple
once it is understood that it is very unlikely that this type
compressor will ever fail. BD compressors have almost an unlimited
life because their control module protects it from failures common
in other hermetic electric compressors. The number one cause for a
Danfoss BD compressor module to terminate a compressor start up is a
low voltage spike. Voltage spikes at module are not always visible
with a meter and can be present on any [boat/motorhome]. Unstable
voltage is why the module must receive power direct from battery
buss using correct size wiring, fuses, circuit breaker and switches
that allow no voltage drop. When the compressor is correctly wired
to the battery buss it will absorb voltage surges like a very large
electrical capacitor reducing module electronics false starts and
module failures.
In my case, the
low-voltage code was flashed on the LED, despite connecting 4 different
power supplies which by-passed the boats power supply cables.
After some days, it dawned on me that the only common factor present
during all tests and trial runs was a 12" long manufacturers cable to
the control box and to the thermostat. When I replaced those, the
'fridge started to work again. So, it is imperative that ALL the
wiring between batteries and control box are checked.
